100吨电子汽车衡准确性保障策略:多维度质量管控方法
时间:2025/4/8 10:00:00 点击次数:213
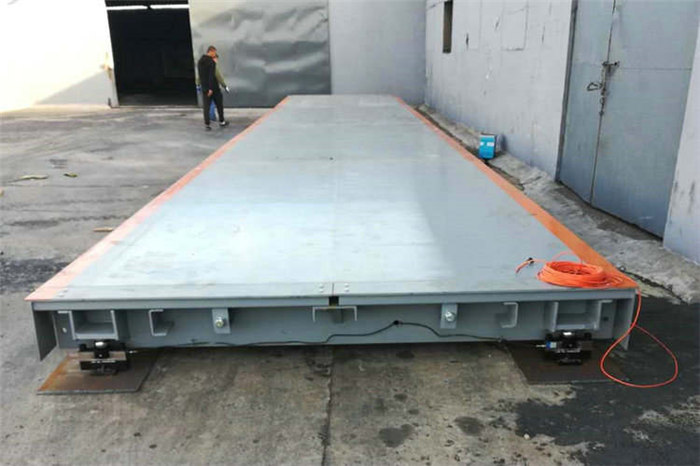
为确保100吨电子汽车衡(电子地磅)的长期准确性,需从设计选型、安装调试、日常使用、维护校准及环境管理等多维度实施系统化质量管控。以下是分阶段、全流程的保障策略:
一、设计与选型阶段
传感器选型与冗余设计
选用高精度应变式传感器(C3级及以上),量程覆盖150%额定载荷(如100吨地磅选用单传感器25吨×8只)。
冗余布局:采用多传感器并联(如8~10个),即使单个传感器失效仍可维持基本功能。
结构强化
秤体采用全钢结构+模块化设计,抗扭刚度≥1/1000,防止长期负载变形。
动态称重场景需增加减震装置(如橡胶缓冲垫)。
信号系统抗干扰
传感器电缆采用双层屏蔽线,仪表端加装信号隔离器。
数字式传感器优先(如RS485输出),减少模拟信号传输损耗。
二、安装与调试阶段
基础施工质量控制
地基承载力:≥150kPa,混凝土厚度≥30cm,预留排水坡度。
水平度:秤体安装后整体水平偏差≤±2mm(使用激光水准仪校准)。
传感器受力均衡调试
偏载测试:用标准砝码依次压载每个传感器区域,调整支座高度使各点输出误差≤0.1%F.S。
全量程标定
分段标定:20%、50%、80%、100%量程点校准,非线性误差≤±0.02%F.S。
动态补偿标定:模拟车辆以5km/h通过,修正速度-重量关系曲线。
三、100吨电子汽车衡日常使用管理
标准化操作流程
静态称重:车辆完全静止后延时3秒读数,避免振动干扰。
动态称重:车速严格控制在3~5km/h,安装红外测速仪联动报警。
数据交叉验证
定期比对:每周用已知重量车辆(如满载卡车)进行实物校验,偏差>0.1%时触发校准。
多仪表冗余:关键场合配置双仪表独立显示,差异>0.05%时停机检查。
超载防护
硬件限位:设置机械挡板阻止150%以上超载。
软件预警:实时显示载荷百分比,超105%自动锁屏并声光报警。
四、维护与校准体系
周期性维护计划
项目 频率 操作标准
传感器零点检测 每日 空载零点漂移≤0.05%F.S
接线端子检查 每周 阻值变化≤0.1Ω
秤体清洁润滑 每月 无杂物堆积,关节部位润滑
防雷接地检测 每季度 接地电阻≤4Ω
智能诊断系统
部署物联网监测模块,实时上传传感器输出、温度、电压等数据,AI算法预测潜在故障(如某传感器输出突降20%提示损坏风险)。
第三方强制检定
每年委托计量院按JJG 539-2016《数字指示秤检定规程》进行全项检测,重点核查:
重复性误差(≤0.05%F.S)
蠕变误差(15分钟漂移≤0.02%F.S)
五、环境适应性控制
温度补偿
选用-30℃~+70℃宽温传感器,仪表内置温度补偿算法。
极寒地区加装秤体加热膜,防止结冰影响受力。
防风防雷措施
加装侧向防风围栏(降低10m/s风速引起的误差至0.02%以内)。
独立避雷针+SPD防雷器,确保雷击残压<1kV。
防作弊设计
传感器密封防护:采用环氧树脂灌封,防止恶意加装遥控装置。
数据溯源:称重记录自动加密存储,绑定车辆RFID标签与监控视频。
六、人员培训与责任追溯
分级培训体系
操作员:掌握标准化称重流程与异常识别(如仪表闪烁ERR-05代码提示传感器故障)。
维护工程师:精通传感器更换与参数标定,持计量检定员证上岗。
全生命周期档案
建立每台汽车衡的电子档案,记录每次校准、维修、比对数据,实现质量追溯。
七、100吨电子汽车衡技术升级路径
趋势技术应用:
5G+边缘计算:实现毫秒级动态称重数据实时处理。
数字孪生:虚拟模型模拟不同工况下的秤体形变,优化校准参数。
通过以上多维度的管控,100吨电子汽车衡可长期保持±0.1%以内的静态精度和±0.5%以内的动态精度,满足贸易结算级称重要求。关键点在于预防性维护+智能化监测+标准化操作的三重保障机制。